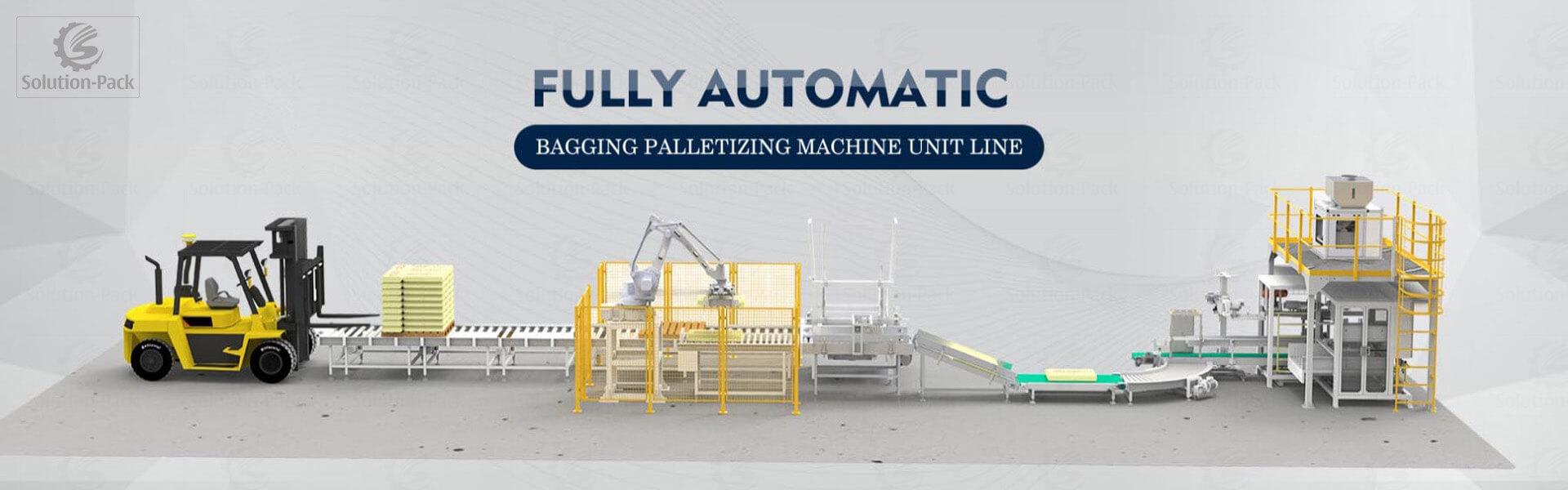
Model HTB-Z50B automatic weighing bagging palletizing machine solution is an integrated bulk bagging machine line to pack 50 kg woven sacks and then palletize them on the pallet automatically. This industrial packaging solution is composed of the HTB-Z50B bagging automatic bagging machine, the heavy-duty conveyor line, ABB Robot palletizing system, and the pallet bank system. The whole system is connected tightly with full-line PLC control. It is widely applied in the seeds, grains, animal feed, aqua feed, sugar mill, urea granule, compound fertilizer, and other related granule products market. It offers a stable production capacity of around 600 bags per hour for users.
Features of Automatic Weighing Bagging Palletizing Machine Solution
The HTB-Z50B automatic weighing bagging and palletizing machine could realize the function of automatic dosing, bag feeding, bag clamping, material filling, bag conveying, bag mouth sealing, bag pushing down, bag flattening, pallet dispatching, and robot palletizing. According to the production requirements, the online weight checking & rejecting system, metal detecting & rejecting system, online inkjet printing system, and pallet online wrapping system could also be equipped to meet the production needs. The weighing filling system could connect with the user’s raw material silo to realize continuous production.
This automatic bagging machine solution adopts a high-standard configuration. All the PLC control and HMI display adopt the industrial Germany Siemens brand. The other electrical and pneumatic parts also use internationally famous brands like SMC Cylinders, SMC Solenoid Valves, Becker Vacuum Pumps, Siemens Servo Motors, Mettler Toledo Load Cells, Schneider Indicators, Omron Proximity Switches, etc. It allows the user to source the easy tear spare parts from the local market easily although the user could purchase from Solution-Pack directly. The whole machine frame is made of coated carbon steel and the material contacting parts is built of stainless steel.
Robotic Bag Palletizing Production Layout
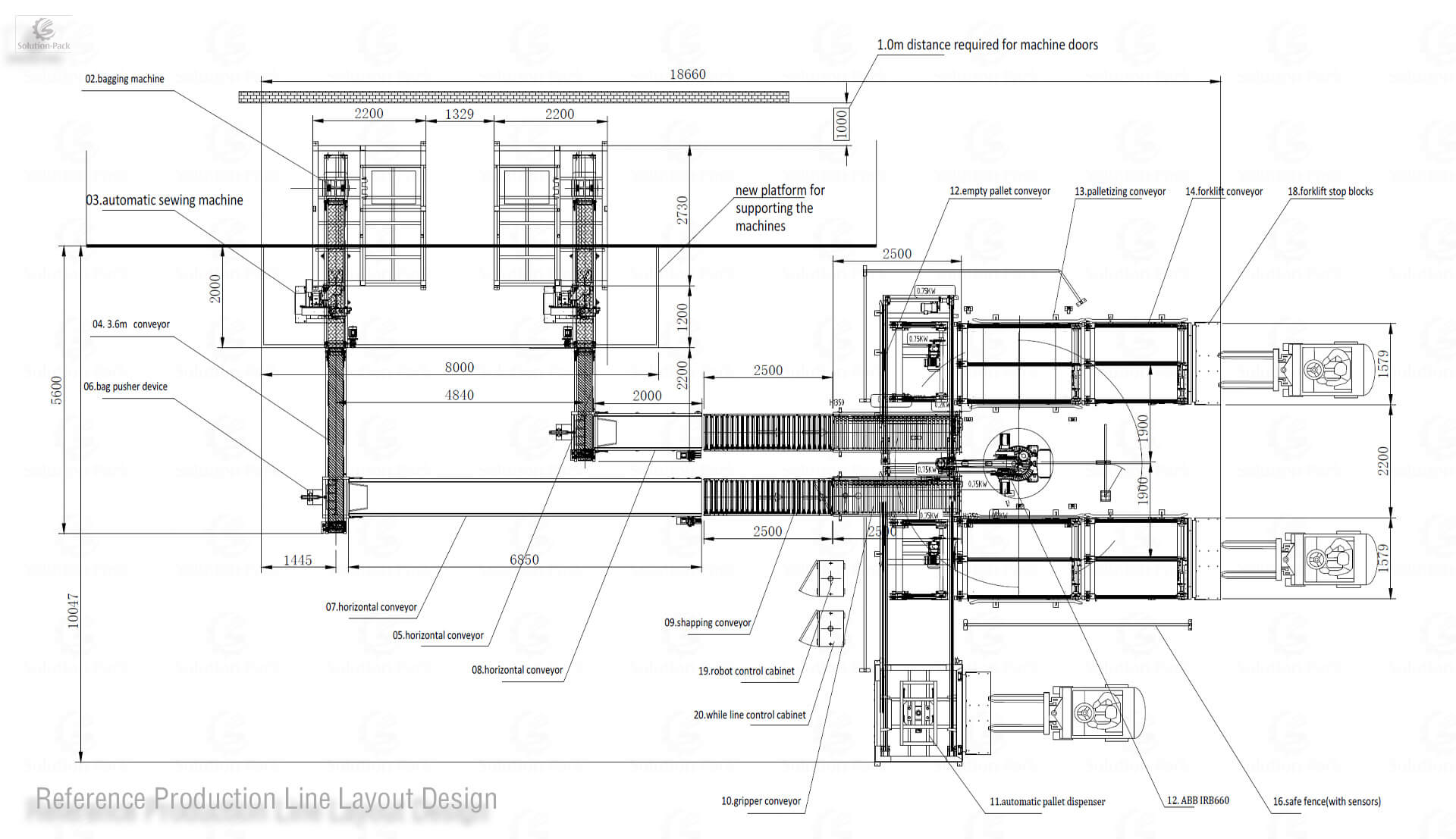
Customized Solution Design
The single woven sack bagging machine system could produce 600 bags per hour which is not realistic to use manually to palletize. When connected with the automatic robot palletizing system, there are two types of combinations according to the target production capacity. The first choice is to connect one bagging stitching system with one ABB460 robot palletizing system and the second choice is to combine two bagging sewing machine systems with one ABB660 robot palletizing system. Which option is more suitable for production shall depend on the user’s warehouse space and required packaging speed.
Life-Long Technical Service
As for all the bagging sealing palleting machine lines from Solution-Pack, we shall send the professional engineer to the user’s warehouse to do the installation and training work for over half a month time to ensure the operator gets the operation and maintenance skills. One-year easy tear parts shall be prepared and delivered with the machine together for the user. And we shall provide life-long technical service for the user whenever they meet issues in machine operation or further spare parts stocking. Each machine unit shall have specific tracking no. to ensure the correct service in future maintenance work.
More Detailed View of The Production Line
Submit Here to Request An Offical Quotation
FAQ about The Weighing Bagging Palletizing Machine
What is a bagging palletizing machine?
The industrial bagging and palletizing machine is a packaging solution to bag bulk material into woven sacks and then use the robot palletizer machine to palletize them on wooden or plastic pallets for easy marketing and transportation.
What is a palletizing system?
A palletizing system is a mechanized machine that follows the order from the PLC to stack the products onto the pallet in a preset pattern. Changing the grasping hand, it could work for both bags, cartons, or even buckets.
How to choose the bag palletizer model?
The bag palletizer model is normally decided by the front-line production capacity. Generally speaking, the bigger the model is, the higher the working capacity.